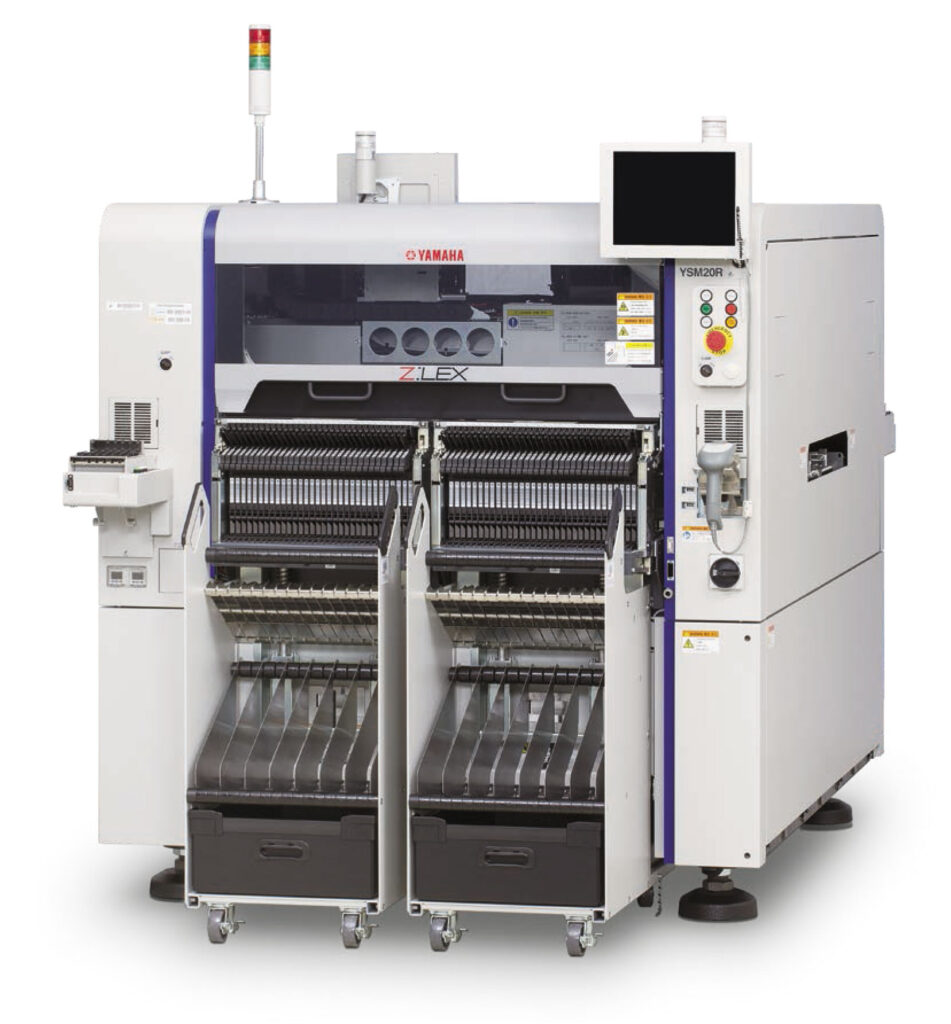
We offer our clients comprehensive cooperation in the field of Electronics Manufacturing Services (EMS) using modern production lines. It includes both serial and prototype orders. We cooperate with both global companies and smaller, developing ones. In order to ensure the highest possible quality, we use quality verification systems at every stage of assembly. They include two-stage AOI control and soldering tests; depending on the customer’s requirements, we can also conduct functional, environmental and many other tests for each project. We guarantee confidentiality of cooperation, and highly qualified staff ensure that assembly processes are carried out in full compliance with ESD conditions and meet the requirements of IPC-A-610 standards.
SMT assembly
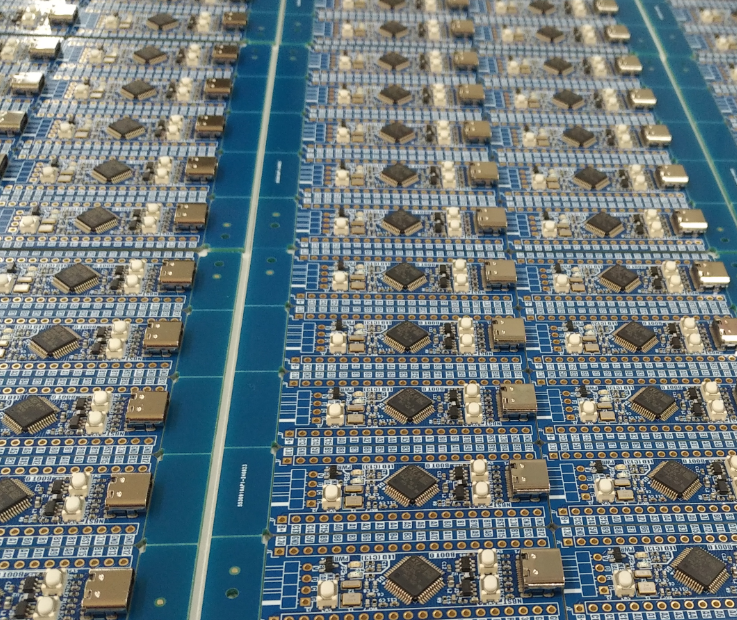
We have two independent SMT assembly lines.
Line 1 is built on the basis of a 10-head Yamaha YRM20 machine with a capacity of up to 49,000 CPH (IPC9850: 33,500 CPH) with the possibility of using 128pcs of 8mm feeders.
Line 2 is built on an 8-head Assembleon MG-1 machine and an 8-head Assembleon Opal XII machine with a total capacity of up to 41,700 CPH (IPC9850: 31,300 CPH) with the possibility of using 196pcs 8mm feeders. Both lines allow for precise, repeatable assembly of elements from size 01005.
The monthly capacity of our lines is 16,000,000 components.
Both lines are equipped with Yamaha stencil screen printers for solder paste (models: YCP10 and YSP) with built-in stencil cleaning systems during operation and optical control of the paste applied to the printed circuit board.
Reflow soldering is carried out in a convection, 7-zone Heller 1707 MK III oven.
THT assembly
For THT assembly, we use the EBSO SPA400-NC selective soldering, in which lead-free soldering takes place in a nitrogen atmosphere. We perform additional through-hole assembly and cable harnesses manually.

Quality check
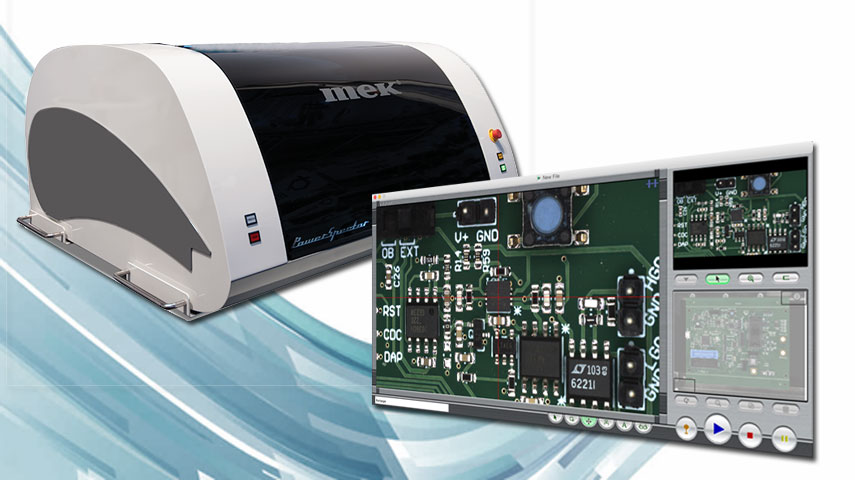
During the assembly of electronics, the quality checks are performed. In these processes, we use the following technologies:
SPI (Solder Paste Inspection) – screen printers are equipped with automatic quality control of the solder paste position on the printed circuit board.
AOI (Automated Optical Inspection) – after soldering is completed, the boards are verified using optical technologies in terms of the correctness of the components used, their arrangement and assembly quality. For this purpose, we use AOI operating in the Viscom line and the independent, offline MEK (Marantz) PowerSpector system.
Depanelization and PCB milling process
The laminate depanelization process includes breaking V-Cut’s and removing drilled bridges using a dedicated, numerical IPTE spindle milling machine. The process is supported by ionization of air in the working chamber. A dust generated during milling is continuously removed using a high-performance Ruwac vacuum system.
At the customer’s request, it is possible to mill edges and shapes in the laminate.
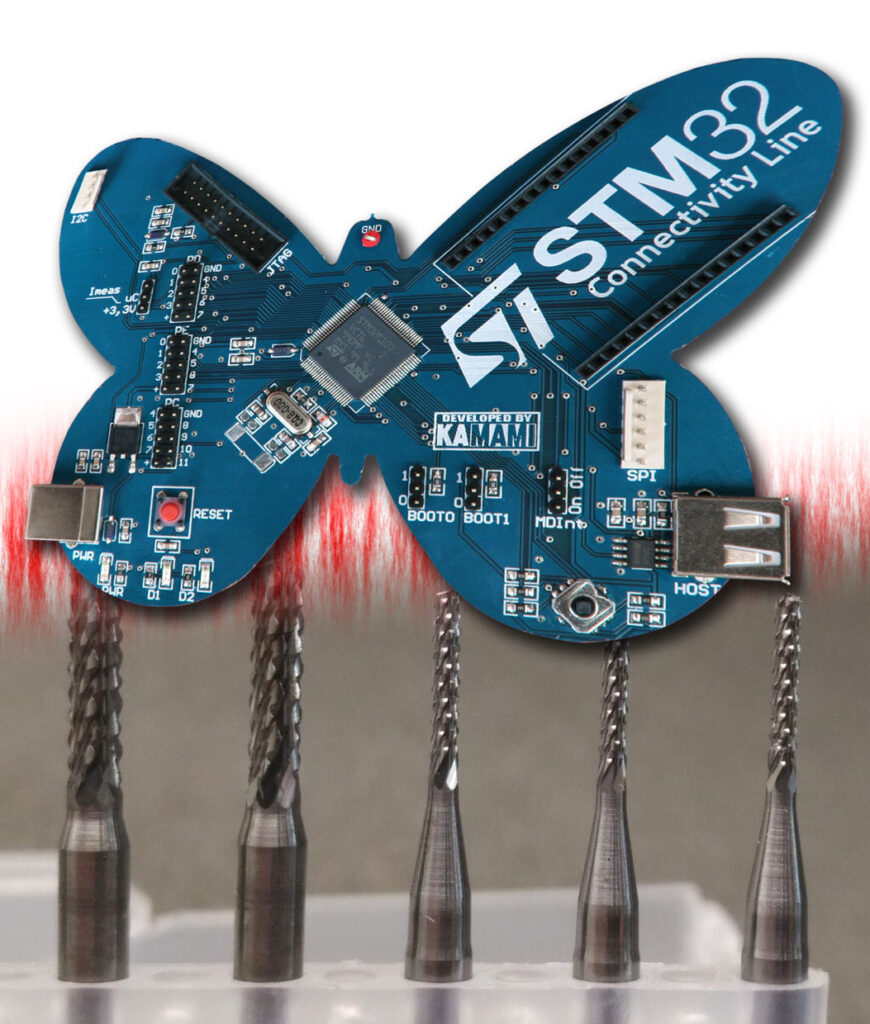
Products marking
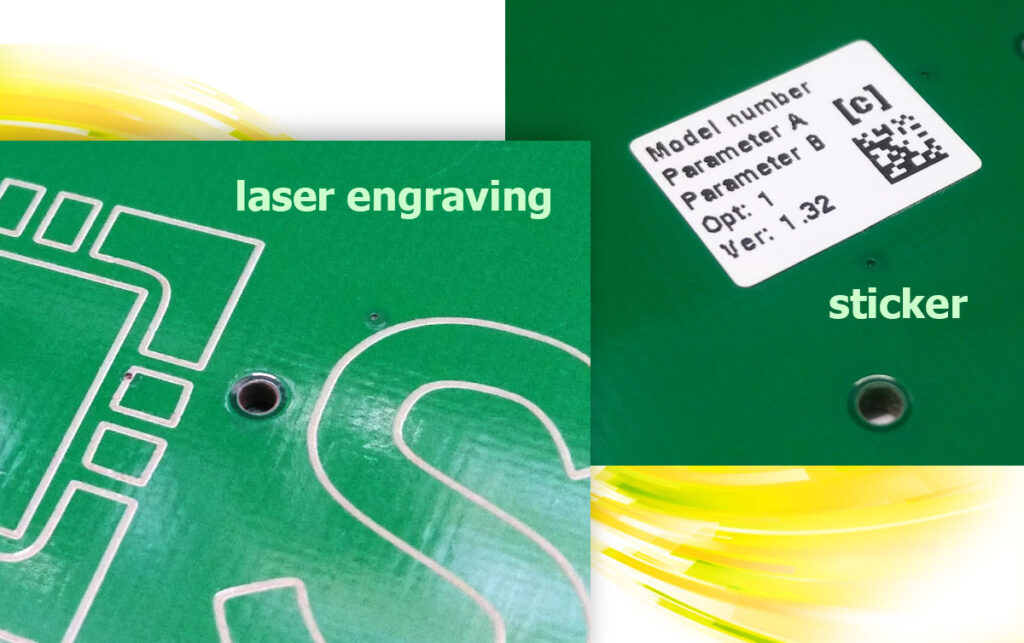
At the customer’s request, we mark electronic boards using thermal transfered labels. Those labels are washing and high temperatures resistant. We also offer permanent laser marking, directly on the laminate.
Logistic
We help our clients choose electronic components or substitutes available on the market. Cooperation with global distributors provides us with quick access to a wide range of electronic components.
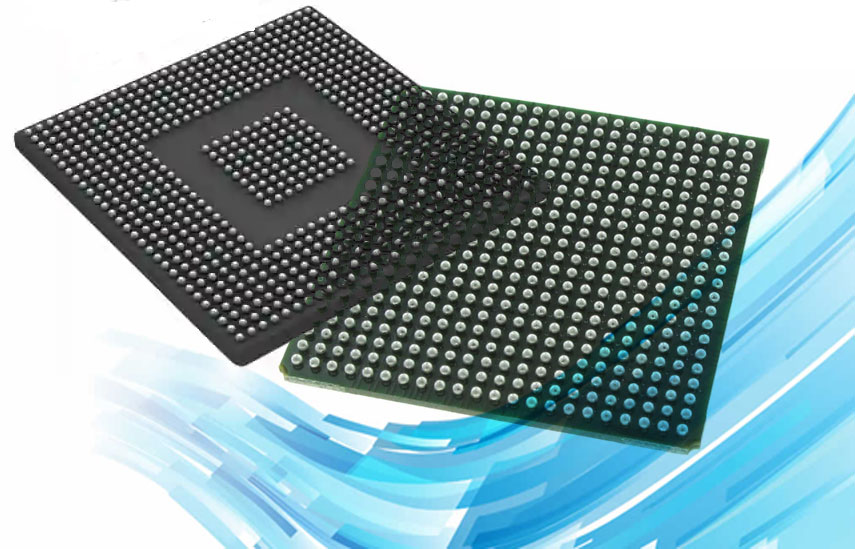